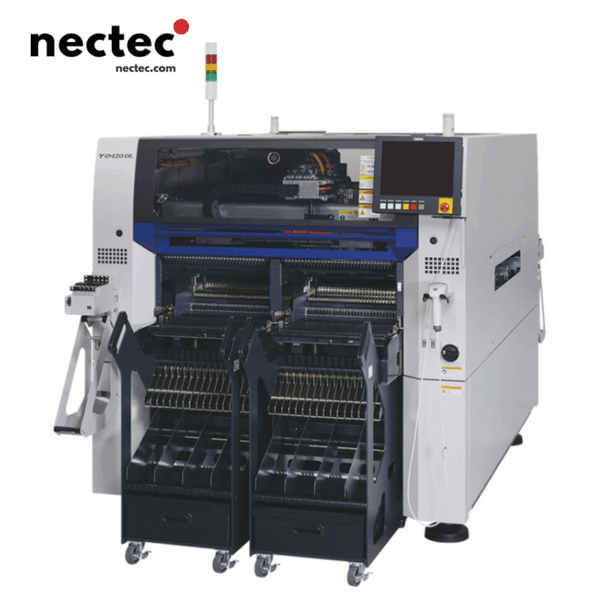
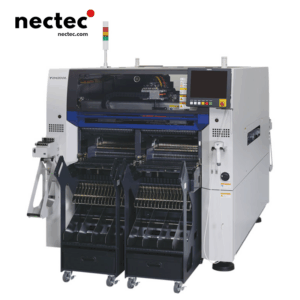
YRM20DL | Super High Efficiency Dual Lane Modular Placement Machine
The YRM20DL is a dual track surface mount machine with excellent productivity, flexibility and PCB placement capabilities. It provides a wide range of production capabilities as a single head solution, suitable for multi-variety and multi-batch production. It can achieve high-precision placement and stable production of micro components.
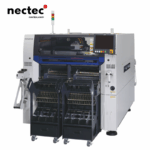
YRM20DL | Super High Efficiency Dual Lane Modular Placement Machine
- Description
Description
Placement Head System
Multi-Configuration Placement Architecture
-
RM Ultra-High-Speed Turret Head (18 Nozzles):
- Achieves 120,000 CPH peak throughput (IPC-9850 compliant) for 0201 metric (0.25×0.125mm) micro-components up to 12×12×6.5mm (L×W×H).
- Turret design enables high-speed rotational pickup with integrated vision for real-time component pose detection, supporting dense placement of ultra-small parts without head changeover.
-
HM High-Speed In-Line Head (10 Nozzles):
- Delivers 100,000 CPH for chip components, handling 0201 metric to 55×100×15mm components (BGA, CSP, connectors).
- Intelligent path planning via embedded scanning camera reduces idle time for medium-to-large component placement.
-
FM Odd-Form In-Line Head (5 Nozzles):
- Supports 03015 metric (0.3×0.15mm) to 55×100×30mm components with force control (0.1–10N), ideal for high-precision connectors and press-fit components.
-
Unified Head Platform: Seamlessly transitions from 0201 metric to 100mm components without head change, minimizing changeover time for high-mix production.
Feeder System
Multi-Modal Material Handling
-
Reel Feeding:
- Fixed feeder rack supports 128 stations (8mm tape equivalent), compatible with 8–56mm pneumatic feeders (F1/F2) and 8–88mm electric feeders (F3).
- AutoLoading Feeders reduce material change time by 30%; ZS/SS smart feeders (YS series compatible) enable offline presetting and continuous feeding.
-
Tray Feeding (Optional):
- eATS30 automatic tray changer supports 30-layer JEDEC-standard trays for non-stop component supply in high-changeover environments.
-
Stick Feeding:
- Single-stick feeders accommodate manual/auto-loading of odd-form components (connectors, heat sinks).
-
Flexible Changeover: Supports 4×CFB-45E material carts (128-station max), enabling mixed 新旧 trolley use for multi-variety production.
PCB Processing System
High-Flexibility Substrate Handling
-
Size Range:
- Single-track: 50×50–810×510mm (industrial PCBs)
- Dual-track: 50×50–810×330mm (parallel processing of mixed/identical boards)
-
Dynamic Transmission:
- 900mm/sec transport speed with laser-guided width adjustment (no mechanical stops), compatible with routed/odd-shaped PCBs.
- Front-reference clamping ensures ±0.1mm positioning accuracy, preventing placement drift.
-
Dual-Track Modes:
- Parallel: Simultaneous processing of dissimilar boards (e.g., smartphone + automotive PCBs).
- Alternating: Double throughput with identical board production.
- Mixed: Flexible combination for complex scheduling.
Vision & Inspection System
Advanced Quality Assurance
-
Component Verification:
- Side-view camera monitors nozzle-tip component pose, detecting missing parts, tombstoning, and skew with ≥99.9% defect rejection rate.
- Embedded scanning camera achieves <0.1s/component high-speed inspection for ≤12mm components (e.g., BGA).
-
Optional Metrology:
- Coplanarity detection for QFP leads (±15μm accuracy) reduces high-end package (SiP) solder defects.
-
Maintenance Integration:
- Auto nozzle cleaning station removes contaminants; RFID-tracked nozzles auto-flag wear.
- Real-time negative pressure sensing verifies pickup integrity post-suction.
Motion Control System
Precision Mechanics
- Drive Technology:
- X/Y axes: AC servo motors + linear guides achieve ±15μm placement accuracy (Cpk≥1.0), ±10μm repeatability for ≤0.3mm pitch components.
- Laser-measured substrate warpage enables dynamic Z-axis adjustment, limiting impact force to ≤50gf for flex PCBs and micro-components.
- Intelligent Path Optimization:
- AI-driven shortest-path planning reduces air travel by 20%, enhancing single-board productivity.
Core Systems & Automation
Software & Connectivity
- Production Orchestration:
- CAD-to-program auto-conversion shortens NPI time by 50%; multi-language HMI (EN/JP/KR/CN) simplifies operation.
- Yamaha Smart Factory integration enables real-time data upload (placement coordinates, OEE) for automotive-grade traceability.
Hardware Design
- Compact Dual-Track Footprint: 1,374×2,102×1,445mm dimensions with 2,550kg mass optimizes floor space in high-density lines.
- Tool-Less Maintenance: One-touch nozzle bracket replacement; auto-cleaner supports batch maintenance (40% time savings); feeder self-diagnostics with real-time fault alerts.
Automation Features
- Auto-Ejector Adjustment: Program-driven ejector positioning adapts to varying board thickness and component layouts.
- Uninterrupted Material Flow: eATS30 tray feeders + auto-reel changers enable lights-out production for extended runs.
specification
RM head | HM head | FM head | |
Super high-speed rotary | High-speed general-purpose in-line | Flexible head for odd shaped chips | |
Nozzles, per 1 head unit | 18 | 10 | 5 |
Applicable components | 0201mm to W12xL12 mm Height 6.5 mm or less | 0201 mm to W55xL100 mm Height 15 mm or less | 03015 mm to W55xL100 mm Height 30 mm or less |
Mounting capability (under optimum conditions) | 120.000 CPH (In high production mode) | 100.000 CPH (In high production mode) | 2-beam: 35.000 CPH 1-beam: 17.500 CPH |
Mounting accuracy | ±15 μm Cpk ≥ 1.0 (high-accuracy mode) | ±35μm Cpk ≥ 1.0 (high-accuracy mode) | |
Number of component types | Feeder carriage exchange: Max. 128 types = 32 feeders x 4 (conversion for 8 mm tape feeder) Fixed plate: Max. 128 types (conversion for 8 mm tape feeder) Trays: 60 types (maximum when equipped with eATS30 x 2) | ||
PCB dimensions | Dual lane use: W50 x L50 mm to W330 x L810 mm | ||
Single lane use: W50 x L50 mm to W610 x L810 mm | |||
Power supply | 3-phase AC 200/208/220/240/380/400/416 V ±10% 50/60 Hz | 3-phase AC 200/208/220/240/380/400/416 V ±10% 50/60 Hz | 3-phase AC 200/208/220/240/380/400/416 V ±10% 50/60 Hz |
Air supply source | 0.45 MPa or more, in clean, dry state | 0.45 MPa or more, in clean, dry state | 0.45 MPa or more, in clean, dry state |
External dimensions (excluding projections) | L 1,374 x W 2,102 x H 1,445 mm | L 1,374 x W 2,102 x H 1,445 mm | L 1,374 x W 2,102 x H 1,445 mm |
Weight | Approx. 2.550 kg (main unit only) | Approx. 2.550 kg (main unit only) | Approx. 2.550 kg (main unit only) |
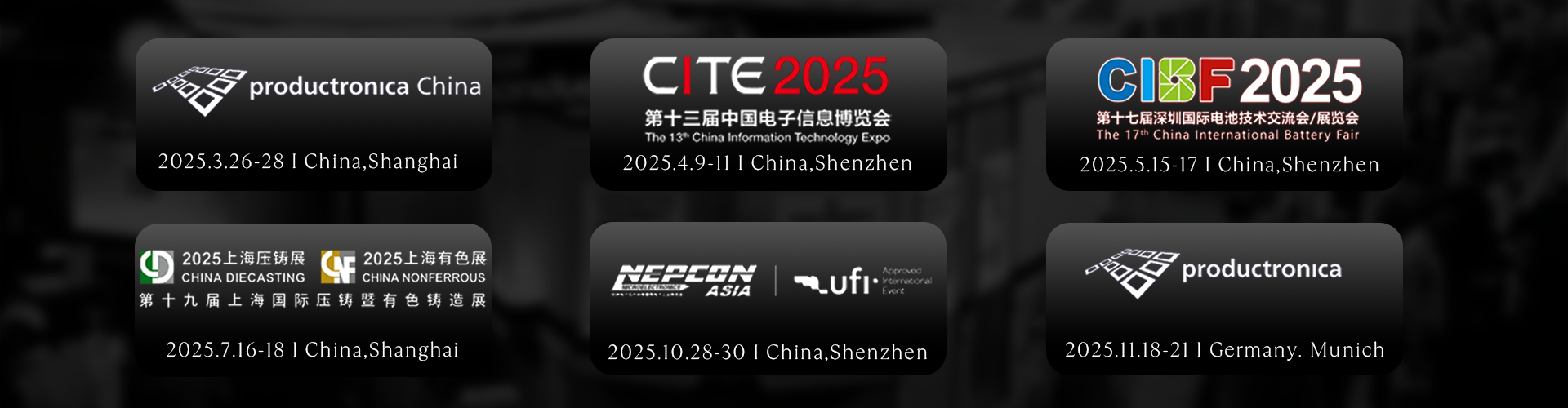