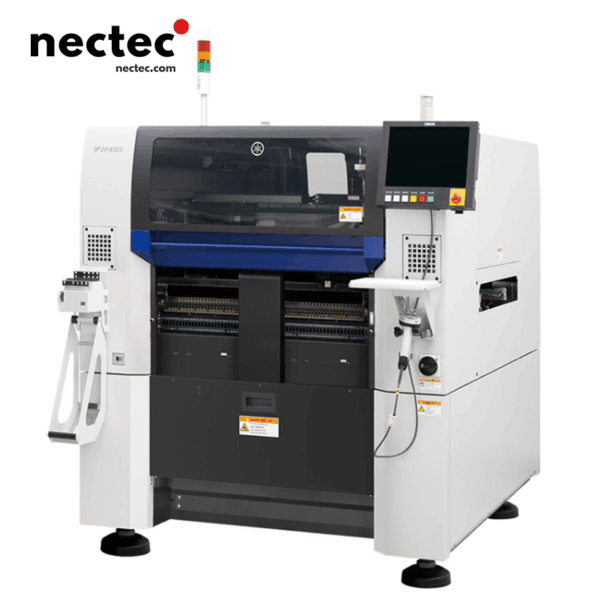
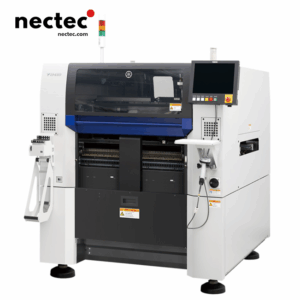
YRM10 | Compact High-Speed Modular
Yamaha’s YRM10 model is equipped with the advanced technology of the YRM series high-end system. It is a small multi-functional high-speed placement machine with excellent cost performance and high placement capacity, realizing value-added production of economical products, and achieving zero-defect production with high placement accuracy and rich functions. It brings excellent ease of use because of the simple single-head operation.
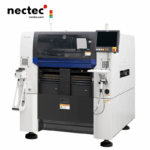
YRM10 | Compact High-Speed Modular
- Description
Description
Placement Head System
High-Speed In-Line Multi-Function Head (HM Head)
- 10-Nozzle Universal Module: Handles 0201 metric (0.25×0.125mm) micro-components to 100×55×15mm odd-form devices (BGA, CSP, connectors) with a peak placement rate of 52,000 CPH (IPC-9850 compliant).
- Precision Engineering: Achieves ±35μm placement accuracy (Cpk≥1.0) via thermally stabilized X-axis beam design, enabling ultra-dense assembly (component spacing ≤0.3mm for 0201).
- Intelligent Operation: Embedded vision camera for real-time component pose detection and dynamic path optimization, reducing air travel by 20%. Supports automatic nozzle change (24-station standard/40-station optional) with RFID tracking for maintenance traceability.
Defect Prevention
- Side-View Inspection: Detects chip component misalignment (skew, tombstoning) with ≥99.9% accuracy to prevent defective placement.
- Optional Coplanarity Gauge: Verifies lead flatness for tray-mounted components (e.g., QFP) to avoid solder joint defects.
Feeder System
High-Density Feeding Solution
- Reel Feeding Capacity: Supports 96 stations (8mm tape equivalent), compatible with 8–56mm pneumatic feeders (F1/F2) and 8–88mm electric feeders (F3) for continuous material flow.
- Tray Feeding Module (sATS15R): Handles 15 types of JEDEC-standard trays, enabling unattended component supply and reducing manual intervention.
- Modular Feeder Design: Ultra-thin lightweight feeders with AutoLoading technology cut changeover time by 30%; supports mixed legacy/new trolleys (CFB-45E/CFB-36E) for flexible production setups.
PCB Processing System
Versatile Substrate Handling
- Size Compatibility: Standard 50×50–510×460mm; expandable to 950×460mm for industrial PCBs (LED, automotive).
- High-Velocity Conveyor: 900mm/sec transport speed with laser-guided dynamic width adjustment, eliminating mechanical stops for routed/odd-shaped boards.
- Front-Locating Clamping: ±0.1mm positioning accuracy via front reference + vacuum clamping, ensuring stability during high-speed placement.
Vision & Inspection System
Advanced Quality Control
- In-Head Vision Module: 5MP camera enables high-speed inspection (≤0.1s/component) for ≤12×12mm components (e.g., BGA), reducing head travel distance.
- Dual-Sensor Pick Verification: Combines negative pressure sensing and visual confirmation to detect mispicks/over-picks with ≥99.9% reliability.
- Preventive Maintenance: Automatic nozzle cleaning station and RFID-based wear tracking maintain suction stability and prevent placement drift.
Motion Control System
High-Precision Actuation
- AC Servo Drives with Linear Guides: Achieves ±35μm positioning accuracy and ±15μm repeatability, suitable for ≤0.4mm pitch components.
- AI-Driven Trajectory Optimization: Reduces idle time by 15% through component distribution analysis, enhancing single-board productivity.
Core Systems & Integration
Intelligent Software Suite
- Automated Program Generation: CAD-to-Gerber conversion shortens new product introduction (NPI) time by 50%; multi-language HMI (EN/JP/KR/CN) simplifies operation.
- Smart Factory Ecosystem: Real-time data upload (placement coordinates, nozzle status) via Yamaha’s MES-compatible platform, enabling automotive-grade traceability.
Compact Hardware Design
- Space-Saving Footprint: 1,254×1,440×1,445mm dimensions with 1,230kg mass fits dense production lines.
- Tool-Less Maintenance: One-touch nozzle bracket replacement and batch cleaning reduce MTBM (mean time between maintenance) by 40%.
specification
Model | YRM10 |
Applicable PCB | L50 x W50mm to L510 x W460mm(Optionally able to support lengths up to 950 mm) |
Applicable components | 0201mm to L100 x W55mm, Height 15mm or less |
Mounting capability (Under our optimized conditions) | 52,000CPH |
Mounting accuracy (Under our optimized conditions) | ±0.035mm Cpk≧1.0 |
Number of component types | Reel components : Max. 96 types (conversion for 8mm tape feeder) Tray components : 15 types (when equipped with sATS15R) |
Power supply | 3-Phase AC 200/208/220/240/380/400/416V +/-10% 50/60Hz |
Air supply source | Over 0.45 MPa, clean and dry state |
External dimension | L1,254 x W1,440 x H1,445mm |
Weight | Approx. 1,230kg (Main unit only) |
Related Products
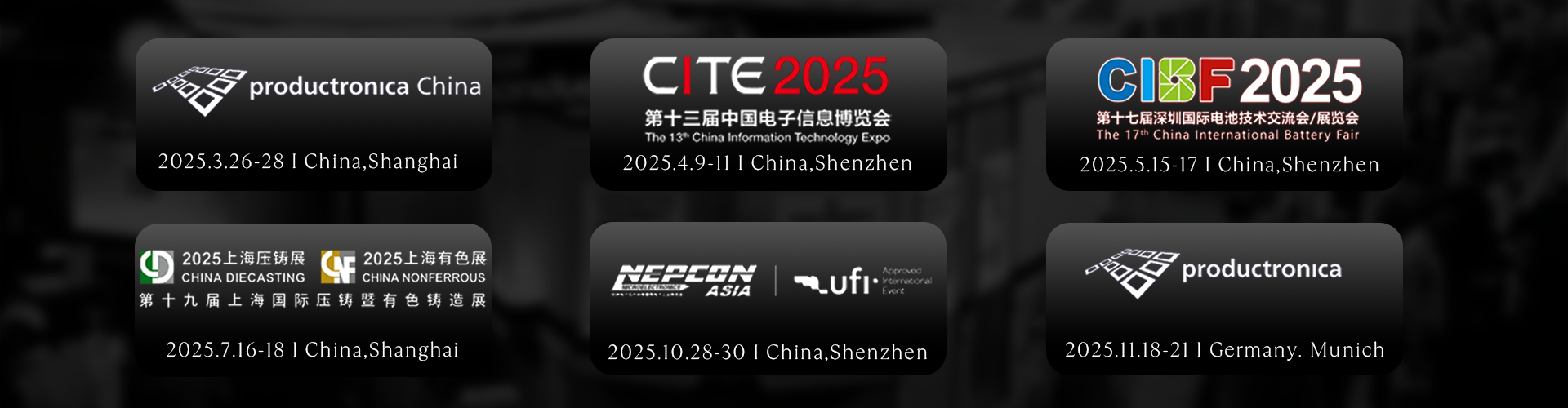