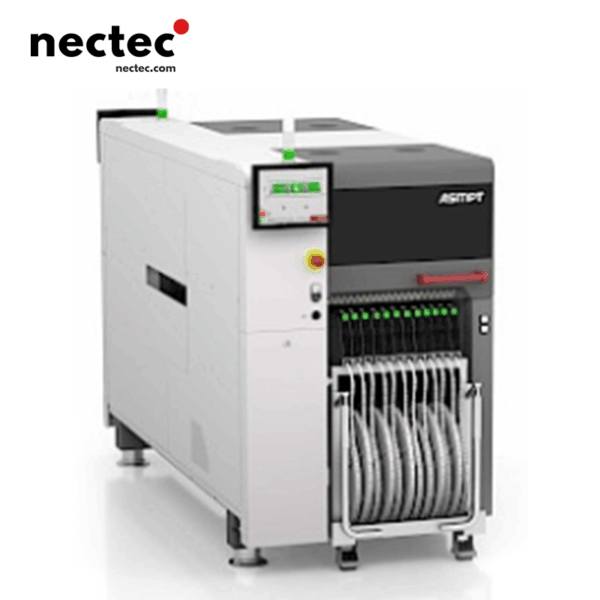
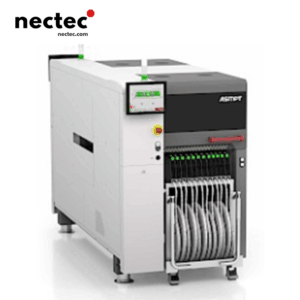
SIPLSCE TX | High Speed Component Placement Machine
The compact SIPLACE TX modules make it very easy to scale your lines up or down. Optimizing each line is less of an undertaking, because getting the perfect balance between requirements and the number of machines is easier than ever.No matter with how many modules you start your line – you can increase its performance in steps of just 1 meter (3.3 feet) or 78,000 cph by adding more SIPLACE TX modules.Maximum accuracy – guaranteed Extremely fast and accurate: With up to 22 µm at 3 sigma, the new SIPLACE TX modules operate with top accuracy.Technological breakthrough: The SIPLACE TX is capable of placing super-fine-pitch 0201 (metric) components at highest speed.This unique combination of accuracy and record-breaking speed makes the SIPLACE TX the clear winner in the race for high-volume 0201 placements.But that‘s not all. No matter how many components you place, our improved control and head technologies protect the machine’s performance and accuracy for years to come.Extremely powerful and designed for the high-volume placement of future component generations, the SIPLACE TX modules deliver the level of investment protection electronics manufacturer want and need for their Smart SMT Factory.
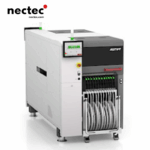
SIPLSCE TX | High Speed Component Placement Machine
- Description
Description
1. Placement Head & Recognition System
- SpeedStar CP20 Multi-Nozzle Head: Handles 0201 metric (0.2×0.1mm) to 8.2×8.2×4mm components at 93,000 CPH with ±20μm accuracy, featuring dynamic pressure control (1.0–15N) for non-destructive placement of sensitive components (e.g., flip chips).
- Dual Cantilever Configuration (e.g., TX micron): Achieves 96,000 CPH via dual-head collaboration (26 cps), supporting high-throughput applications.
- LNC Laser Sensor: Provides real-time ±50μm (Cpk≥1) component profiling for in-flight verification, reducing downtime.
- Blue Light Vision System: Detects BGA solder ball defects and chip cracks with high-contrast imaging, compliant with ISO Class 7 cleanroom standards.
2. Feeder System
- Mixed Feeding Capability: Supports 8–56mm powered feeders, tube/tray components, and JEDEC trays (120-station capacity, 8mm equivalent).
- SIPLACE Tray Device: Accommodates 82 JEDEC/41 wide trays (355×275mm) for non-stop feeding, enhancing continuous production.
- Smart Feeder Technology: Enables automatic material splicing, shortage alerts, and buffer zone management to minimize manual intervention.
3. PCB Processing
- Substrate Handling Range: Standard 300×240mm (15μm@3σ), expandable to 590×460mm for flexible/curved boards and carriers up to 20.5mm height.
- Multifunctional Conveyor: Supports J-boat carriers and JEDEC trays, optimized for high-reliability automotive applications.
- Motorized Support Table: Reduces transport vibration and shortens clamping time for improved placement stability.
4. Software & Automation
- Open Interfaces: Integrates MES/ERP via IPC-CFX/HERMES-9852 protocols for full-process traceability in automotive electronics.
- JaNets System: Enables offline programming, path optimization, and simulation to reduce changeover time to minutes.
- Predictive Maintenance: Real-time sensor monitoring with proactive alerts minimizes unplanned downtime.
5. Technical Advantages
- SiP Production: Integrates 93k CPH SMT placement and 62k CPH die bonding (10μm accuracy), supporting 50μm-pitch passive component placement for high-density packaging.
- Automotive Compliance: Offers material-level traceability, SEMI S2/S8 certification, and harsh-environment reliability.
- End-of-Line Flexibility: TwinHead handles 200×110×25mm, 160g odd-shaped components, replacing robotics with 27.5% floor space savings.
specification
SIPLACE TX1/TX2 | SIPLACE TX2i | |||
Machine dimensions (LxWxH) | 1.00mx2.35mx1.45m | 1.00mx2.23mx1.45m | ||
Placement heads | SIPLACE SpeedStar(CP20P), SIPLACE MultiStar(CPP),SIPLACE TwinStar | |||
Placement speed (benchmark rating) | Up to 78,000 cph | |||
Placement accuracy | Up to 22 μm at 3 sigma | |||
Component spectrum | 0201 (metric) to 45 mm x 55 mm | |||
PCB dimensions (LxW) | 45 mm x 45 mm to 375 mm x 260 mm (dual conveyor) 45 mm x45 mm to 375 mm x 460 mm (dual conveyor in single mode) | |||
Feeder slots | up to 80 x 8 mm | |||
Typical power consumption | 1,9 kW (2 x SIPLACE SpeedStar) | |||
Air consumption | 120 NI/min (2 xSIPLACE SpeedStar) | |||
Placement heads | SIPLACE SpeedStar (CP20P) | SIPLACE Multi Star | SIP LACE TwinStar | |
Component spectrum | 0201 (metric) to 6 mm x 6 mm | 01005 to 50 mmx 40 mm | 45 mmx55 mm | |
Component height | 4mm | 11.5 mm | 25 mm | |
Placement accuracy (3 sigma) | 25 μm | 34 μm | 22 μm | |
Max. Speed | 39,000cph | 24,000 cph | 5,500 cph |
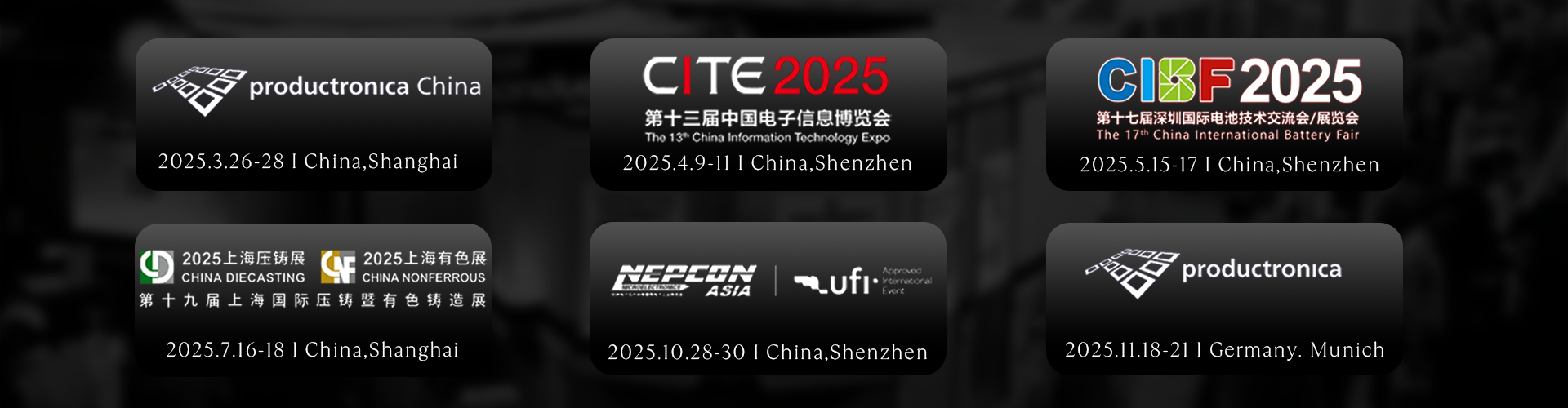