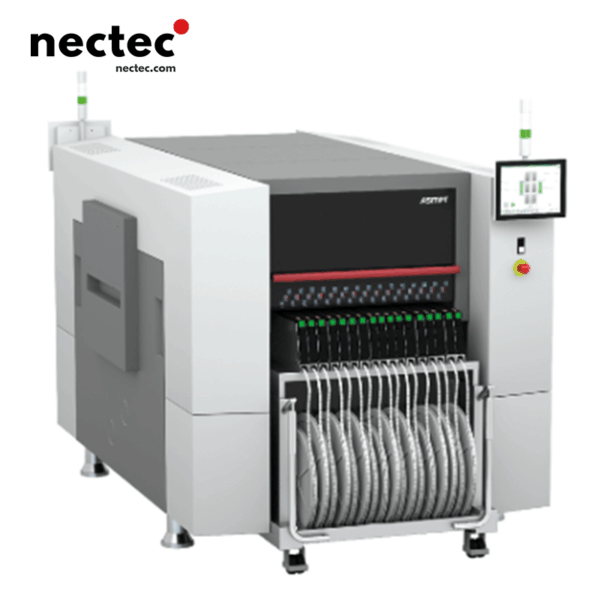
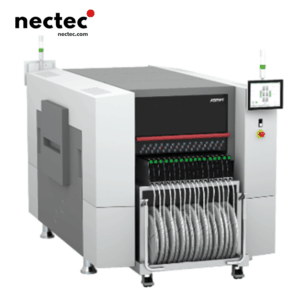
SIPLACE-SX | Cantilever modular placement machine
SIPLACE SX is the first placement solution that is fully scalable with demand thanks to its unique interchangeable gantries. A great way to add capacity when needed or reduce capacity when things slow down. We call it ASMPT Capacity-on-Demand.The SIPLACE SX-Series puts scalability and flexibility at the top of the list. Users are able to introduce new products quickly, change setups without stopping the line and produce any batch size with high utilization and efficiency.Whether in automotive, automation, medical, telecommunication or IT infrastructure – the ASMPT SX-Series meets all requirements in terms of quality, process reliability and speed.
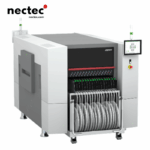
SIPLACE-SX | Cantilever modular placement machine
- Description
Description
1. Modular Cantilever Architecture & Placement Head System
Cantilever Modularity Design
Diverse Placement Head Configurations
- SpeedStar CP20 Head: Handles 0201 metric (0.2×0.1mm) to 8.2×8.2×4mm components with a placement throughput of 43,250 CPH and ±35μm @3σ positional accuracy, optimized for high-speed/high-precision SMT applications.
- MultiStar & TwinStar Heads: Accommodate large complex components (up to 50×150mm, 240g) with up to 100N placement force, supporting through-hole technology (THT) processes like pin bending.
- CPP Placement Head: Enables pick-collect-mix mode switching, compatible with components ≤15.5mm in height and ≤20g in weight.
2. Vision Inspection System & Imaging Algorithms
High-Resolution Visual Processing
Laser Recognition Technology
3. Feeder System Compatibility Design
Feeding Capacity & Flexibility
4. PCB Processing Capabilities
Substrate Handling & Conveyance
5. Intelligent Software & Automation Interfaces
Smart Operational Features
- Nozzle ID Management: Automatically verifies nozzle condition, enabling intelligent selection/replacement across 320 nozzle positions to prevent misplacement errors.
- Predictive Maintenance System: Real-time sensor monitoring triggers proactive maintenance alerts, reducing unplanned downtime.
- Intelligent Operator Guidance: Stepwise wizards assist with component placement troubleshooting (e.g., height calibration, fiducial mark alignment), minimizing setup time.
Open Automation Interfaces
6. Scalable Application Solutions
Odd-Shaped Component (OSC) Processing Kit
Automotive Electronics Solution
specification
Technical data* | SIPLACE SX1 | SIPLACE SX2 |
Placement speed** | 43,000 cph | 86,500 cph |
Placement speed(IPC) | 33,000 cph | 66,000 cph |
Feeder capacity | 120 x 8mm slots | |
Component spectrum | 0201(metric) to 200 mm x 110 mm x 50 mm | |
Board size | 50 mm x 50 mm to 1,525 mm x 560 mm | |
Machine dimensions (L x W x H) | 1.5mm x 2.8m x 1.8m | |
Placement heads | Placement Head CP20P, Placement Head CPP, Placement Head | |
Placement accuracy | 22 μm @ 3 σ (with Placement Head TH) | |
Conveyors | Single-track conveyor, flexible dual-track conveyor |
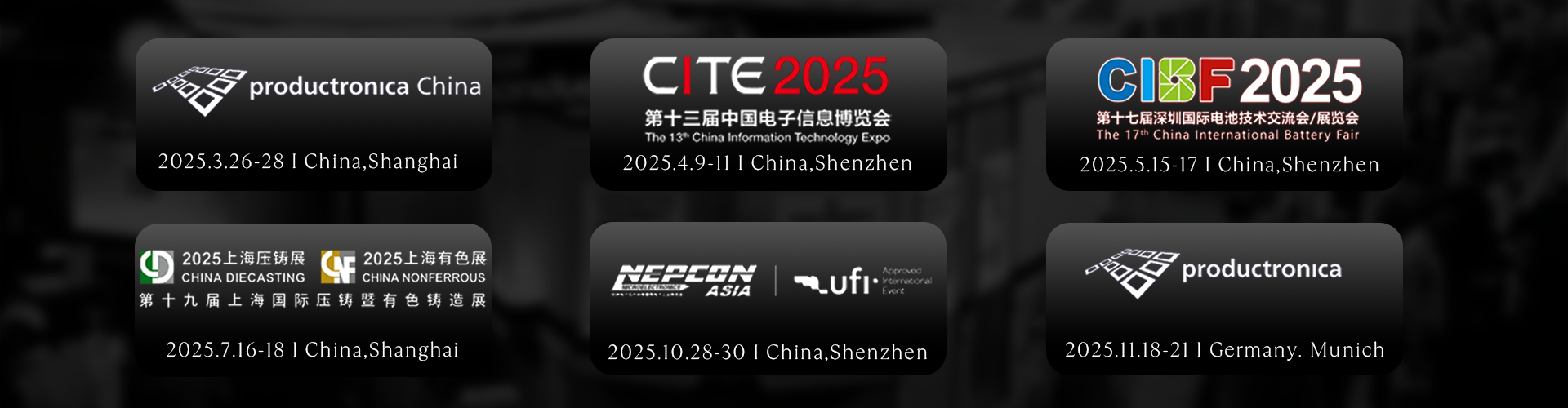