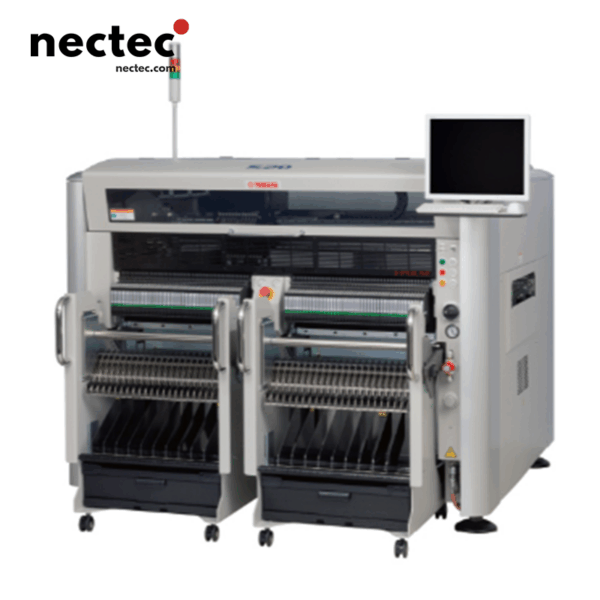
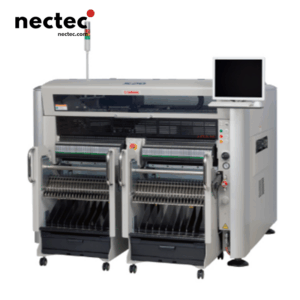
S20 | 3D Hybrid Universal Placement Machine
The Yamaha S20 fulfills the need for higher throughput in the flexible assembly and LED lighting sectors. The new high capacity head system addresses the need for faster cycle times and provides ultra-large PCB handling capabilities with higher placement rates. The highly flexible S20 is available with the new head system incorporating 12 spindles with a wide component handling range. The S20 utilises the same fast change feeder bank and tray handler capabilities as the popular M20 and has a feeder capacity of up to 180 feeder positions. The optional camera will allow placement of parts down to 0.2 x 0.1 mm fulfilling the current demands on reduced component and ball sizes.
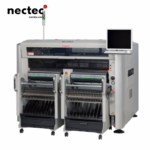
S20 | 3D Hybrid Universal Placement Machine
- Description
Description
Placement Head System
12-Spindle + 2θ-Axis Multi-Nozzle Head
- Hybrid Placement Architecture: Supports mixed placement of 0201 metric (0.2×0.1mm) micro-components to 120×90mm odd-form devices (BGA, CSP, connectors) with a theoretical throughput of 45,000 CPH under ideal conditions.
- Adaptive Z-Axis Control: AC servo-driven dynamic pressure modulation (0.1–50N) adapts to component thickness (up to 30mm) to prevent damage to fine-pitch components.
- Dual-Angle Rotation Capability: ±180° θ-axis rotation ensures precise polarity alignment for polarized components.
Vision & Inspection System
Dual-Precision Metrology Suite
- Tiered Placement Accuracy:
- Class A (Chip Components): ±40μm @ 3σ
- Class B (IC Components): ±25μm @ 3σ (Cpk≥1.33 for fine-pitch applications)
- Combined Vision-Vacuum Verification:
- Image recognition for lead coplanarity and polarity checks.
- Vacuum pickup sensors validate component retention, reducing mispick rates to <0.03%.
- Multi-Sensor Imaging: Standard vision camera + laser profiler enable rapid inspection of chip and odd-form components.
Feeder System
Hybrid Feeding Ecosystem
- Expanded Feeder Compatibility:
- F3 series electric feeders (8–88mm tape)
- F1/F2 series pneumatic feeders (8–56mm tape)
- Stick feeders and JEDEC-standard tray systems
- 180-Station Capacity (8mm Tape Equivalent): Supports simultaneous reel/tray/stick feeding for high-mix production.
- Intelligent Feeding Technology: Auto-tape splicing and real-time shortage alerts minimize manual intervention.
PCB Processing Capability
Ultra-Wide Substrate Handling
- Standard/Extended Dimensions:
- Minimum: 50×30mm
- Standard: 1,455×510mm
- Maximum: 1,830×510mm (LED panel/industrial board compatible)
- Buffer Module Optimization: Entry/exit buffers support 540×510mm PCBs for high-frequency changeover scenarios.
- High-Velocity Conveyor System: 900mm/sec transport speed with active clamping and auto-width adjustment ensures ±0.1mm positioning accuracy.
Motion Control System
Precision Linear Drive Technology
- Magnetic Levitation Drives: X/Y axes with 0.001mm-resolution magnetic scales achieve sub-micron stability (±15μm repeatability) at high speeds.
- Dual-Servo Y-Axis Stabilization: Reduces conveyor vibration by 40% during high-speed placement, ensuring long-substrate positional consistency.
Software & Intelligent Functions
Multilingual Production Platform
- Global HMI Support: Japanese, Chinese, Korean, and English interfaces for cross-regional production management.
- VIOS Automation Suite:
- Real-time placement diagnostics with error correction prompts.
- Integrated path optimization reduces changeover time to <8 minutes.
- Offline Programming Workflow: CAD data import with 3D simulation debugging enhances production efficiency by 25%.
specification
Model | S20 |
Board size (with buffer unused) | Min. L50 x W30mm to Max. L1,830 x W510mm (Standard L1,455) |
Board size (with input and output buffers used) | Min. L50 x W30mm to Max. L540x W510mm |
Board thickness | 0.4 – 4.8mm |
Board flow direction | Left to right (Std) |
Board transfer speed | Max 900mm/sec |
Placement speed (12 heads + 2 theta) Opt. Cond. | 0.08 sec/CHIP (45,000 CPH) |
Placement accuracy A (μ+3σ) | CHIP +/- 0.040mm |
Placement accuracy B (μ+3σ) | IC +/- 0.025mm |
Placement angle | +/- 180 degrees |
Z axis control/ Theta axis control | AC servo motor |
Component height | Max 30mm*1 (Pre-placed components: max 25mm) |
Applicable components | 0201mm – 120 x 90mm, BGA, CSP, connector, etc. |
Component package | 8 – 56mm tape (F1/F2 Feeders), 8 – 88mm tape (F3 Electric Feeders), stick, tray |
Drawback check | Vacuum check and vision check |
Screen language | English, Chinese, Korean, Japanese |
Board positioning | Board grip unit, front reference, auto conveyor width adjustment |
Component types | Max 180 types (8mm tape), 45 lanes x 4 |
Transfer height | 900 +/- 20mm |
Machine dimensions, weight | L1750 x D1750 x H1420mm, Approx. 1450kg |
Related Products
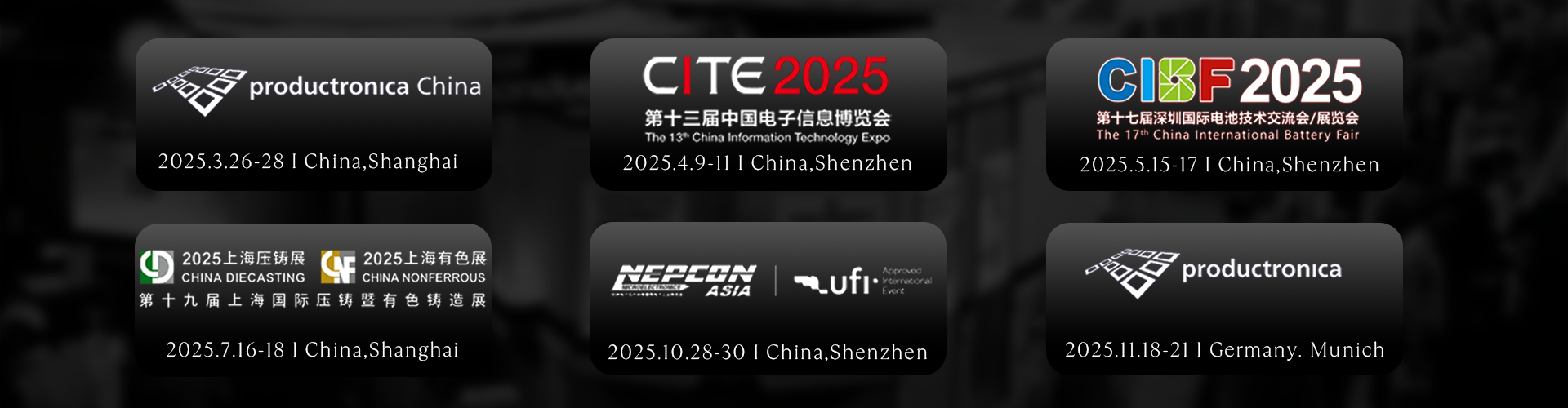