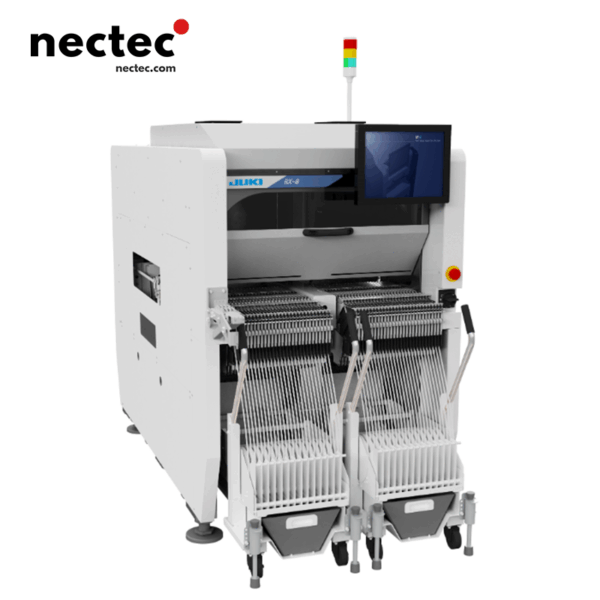
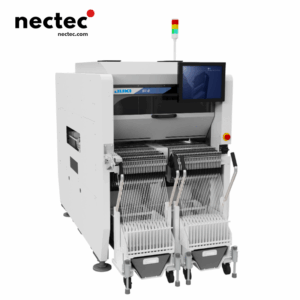
RX-8 | High -Speed Compact Modular Mounter
JUKI RX-8 achieves ultra-high speed (100,000 CPH) and high precision (±40μm) micro-component placement through P20 placement head, high-precision vision system and intelligent feeding management, which is especially suitable for high-density placement scenarios such as consumer electronics and LED lighting. Its compact design and JaNets system support efficient production line integration and process optimization, and is a benchmark for SMT equipment that takes into account speed, precision and flexibility.
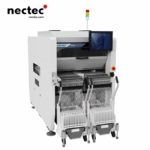
RX-8 | High -Speed Compact Modular Mounter
- Description
Description
Placement Head System (P20 High-Precision Placement Head)
- Throughput Performance:
- Achieves up to 100,000 CPH under ideal conditions for micro-components (e.g., 0201 metric), enabling high-speed single-reel tape pickup and placement.
- Component Compatibility:
- Optimized for ultra-small components (0201 metric and above) and small ICs, handling 0201 to 5mm² components with ≤3mm height, suitable for high-density applications like LED edge lighting.
- Low-Force Placement Technology:
- Independent control of nozzle plunge force (downward pressure) and retraction velocity minimizes impact on components/substrates (especially flex PCBs), ensuring stable micro-component placement.
- Real-Time Vision Correction:
- Integrated advanced centering and inspection vision systems automatically correct post-pick component positional deviations, achieving ±40μm accuracy (Cpk≥1) and reducing flip defects.
- On-The-Fly Inspection:
- Verifies component presence and polarity in real-time before placement, ensuring process compliance.
Vision System
- Coaxial Illumination Technology:
- XO coaxial lighting enhances image clarity for 0201-class micro-components, improving recognition accuracy and stability.
- Multi-Functional Inspection:
- Real-time detection of missing components, misorientation, and automatic pickup position recalibration to enhance pick success rate.
- Fiducial Mark Recognition:
- High-precision substrate fiducial alignment compensates for warpage/positional deviations, ensuring placement consistency.
- Substrate Handling Modes:
- Single Track: 50×50–510×450mm PCBs (BOC, Bad Mark, and 2D barcode reading supported for 50–350mm length).
- Dual Long-Board Mode: Simultaneously processes two ≤420mm-length substrates to optimize dual-board production efficiency.
Feeding System
- High-Density Feeding Architecture:
- Dual 8mm tape reels in single 17mm feeder slots (RF08AS model) enable 56-type feeder capacity, supporting 8–88mm tape and hybrid small-to-large component feeding.
- Adaptive Pickup Calibration:
- Dynamic feeder position adjustment based on component recognition ensures stable pickup.
- Batch Change Trolley:
- Supports mixed electric/mechanical feeder configurations for rapid batch replacement, reducing changeover time.
- Feeder Status Visualization:
- LED indicators provide real-time operational status; fault flashing locates problematic feeders.
- Legacy Compatibility:
- Supports existing mechanical feeders and batch trolleys for asset protection, with optional tape/tray feeding modules.
Motion Control System
- Compact Modular Design:
- Lightweight gantry architecture (998mm width) delivers industry-leading placement efficiency per square meter.
- Precision Mechanics:
- XY-axis repeatability of ±40μm (Cpk≥1); Z-axis height compensation ensures vertical placement accuracy.
- Flexible Substrate Handling:
- Single-track: Up to 510×450mm PCBs; dual-track: Two ≤420×250mm PCBs simultaneously, adapting to mixed-variety production.
- Substrate Stabilization:
- Vacuum chuck and mechanical clamping mechanisms reduce vibration during high-speed placement, enhancing stability.
Software Ecosystem
- End-to-End Process Management:
- Offline programming, multi-machine data sharing, and real-time equipment monitoring (via Factory Dashboard) optimize line balance with CAD data integration.
- Traceability Monitoring:
- Real-time tracking of placement head performance, recording pick errors and anomalies to identify faulty feeders/nozzles for rapid diagnostics.
- Defect Mark Propagation:
- Integrates upstream AOI bad mark data to skip defective PCB areas, reducing re-inspection time.
- Intelligent Material Scheduling:
- Auto-triggered replenishment alerts linked to automated warehousing ensure uninterrupted production.
- Low-Force Placement Setup:
- Adjustable nozzle plunge speed/force for flex PCBs and micro-components to prevent substrate deformation.
- Multi-Lingual Support:
- English GUI and documentation, with optional remote monitoring and diagnostics.
Power & Pneumatics
- Power Supply:
- Three-phase AC 200V/220V (430V with transformer); 2.1kVA apparent power, energy-efficient design.
- Pneumatic Requirements:
- 0.5±0.05MPa air pressure; 20L/min ANR standard consumption ensures stable component pickup/placement.
specification
High -Speed Compact Modular Mounter RX-8 | ||
Specifications | Data | |
Board size | 50×50~510mm×450mm BOC, Bad Mark, and 2D barcode can be read only if board length is from 50mm to 350mm In long board mode (two boards can be produced simultaneously up to 420mm long). | |
Component height | 3mm | |
Component size | 0201~□5mm Please contact JUKI for details. | |
Placement speed (Optimum) | Chip | 100,000CPH |
Placement Accuracy | ±40μm (Cpk ≧1) | |
Feeder capacity | Upto 56 When using RF08AS | |
Power supply | 3-phase AC200V, 220V 430V 220V – 430V requires a separate transformer | |
Apparent power | 2.1kVA | |
Operating air pressure | 0.5±0.05MPa | |
Air consumption (standard) | 20L/ min ANR (during normal operation) | |
Machine dimensions (W x D x H) Depth D does not include the monitor, and height H does not include the signal light when the conveyor height is 900 mm. | 998mm×1,893mm×1,530mm | |
Mass (approximately) | 1,810 kg (with fixed bank)/ 1,760 kg (with bank changing) |
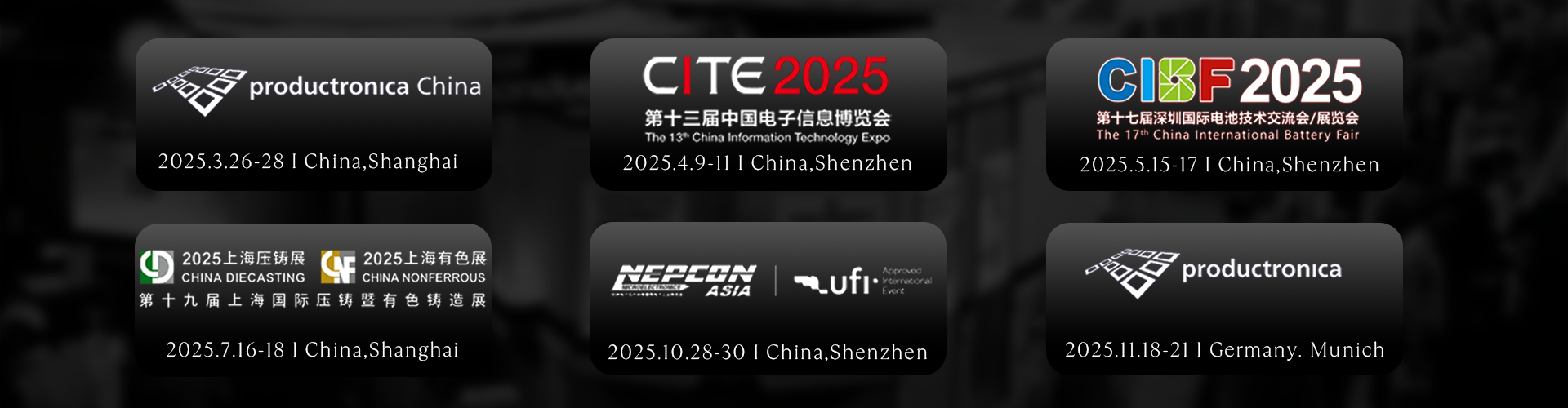