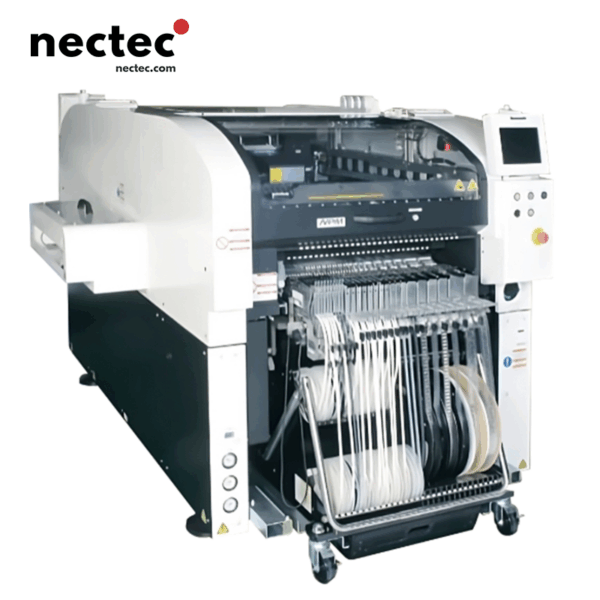
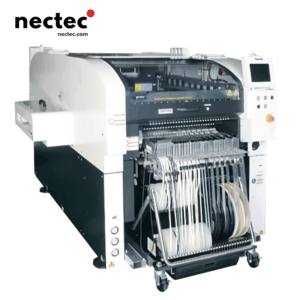
NPM-W2S | High-Flexible Placement Machine
The highly flexible single-beam NPM-W2S is an ideal placement solution for manufacturers who value reduced setup and changeover time over volume… At a time when your lot sizes are getting smaller, customers need to tighten control of work in process, schedule more efficiently and expand feeder capacity. This need is the premise behind the NPM-W2S. The NPM-W2S is based on the NPM-W2 platform, but with the simplification of employing a single beam to access all 120 8mm inputs for increased flexibility, with an output of 38,500 CPH and accuracy of 30um. The NPM-W2S enables customer to afford more platforms per line to increase available feeder capacity for common setups and reduced changeover. The NPM-W2S also makes an affordable line booster at the beginning or end of an existing NPM line.
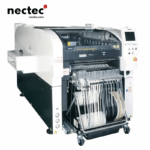
NPM-W2S | High-Flexible Placement Machine
- Description
Description
Panasonic NPM-W2S Single-Beam Placement System
Placement Head System
Multi-Configurable Placement Heads
- Lightweight 16-Nozzle Head: Designed for ultra-high-speed placement of 0201 (008004) to 6×6mm micro-chips, achieving peak throughput in high-density PCB assembly.
- 12-Nozzle/8-Nozzle Heads: Balances speed and versatility for mid-range component sizes (0402 to 12×12mm).
- 3-Nozzle V2 Head: Specialized for odd-form components (up to 74×74mm) with adaptive force control (up to 100N placement pressure), ideal for connectors and large ICs.
- Autonomous Fault Recovery: For 4mm plastic (black), 8mm paper/plastic (black) tape components, the system auto-corrects pick positions without halting production during mispick or recognition errors, minimizing downtime.
Vision Inspection System
Award-Winning Multi-Function Vision Module
- Integrated 3D Metrology: Single-pass component alignment, thickness profiling (±0.01mm accuracy), and coplanarity inspection (±0.02mm for BGA/QFP leads).
- Defect Detection Capabilities: Identifies positional offsets, thickness variations, and lead coplanarity issues to ensure first-pass yield and reduce rework.
Feeding System
High-Capacity Hybrid Feeding Platform
- 120-Station Feeder Bank (8mm equivalent): Supports extended production runs with reduced material changeovers, accommodating reels, trays, sticks, and stacked stick feeding for diverse packaging formats.
- NPM Series Interchangeability: Placement heads, nozzles, tape feeders, and changeover trolleys are fully compatible with existing NPM systems, enabling cost-effective line expansion.
- Flexible Material Handling: Hybrid feeder configuration (reel/tray/stick) with automated stick stack feeding for high-mix, low-volume production scenarios.
PCB Handling System
Dual-Lane/Single-Lane Processing
- Single-Lane Mode:
- Batch processing: 50×50–750×550mm PCBs
- Dual-placement: 50×50–350×550mm (2-up panels)
- Dual-Lane Mode:
- Batch processing: 50×50–750×260mm (dual-track)
- Dual-placement: 50×50–350×260mm (dual-track 2-up)
- Modular Changeover System: 3.5-minute automated module changeovers via feeder auto-switching and program pre-loading, ideal for small-batch, high-mix production.
Auxiliary Systems
PIP (Pin-In-Paste) Vision Module
- Optical inspection of through-hole pin position and lead form (bending) for accurate insertion of THT components, ensuring solder joint integrity.
End-to-End Traceability System
- Lot-Level to Reference Designator Tracking: Full-process monitoring from work order to component level, enabling real-time production data analytics, quality traceability, and process optimization via MES integration.
specification
Model ID | NPM-W2S Pick and place machine | ||||
PCB dimensions (mm) | Single-lane | Batch mounting | L 50 x W 50 ~ L 750 x W 550 | ||
2-positin mounting | L 50 x W 50 ~ L 350 x W 550 | ||||
Dual-lane | Dual transfer (Batch) | L 50 × W 50 ~ L 750 × W 260 | |||
Dual transfer (2-positin) | L 50 × W 50 ~ L 350 × W 260 | ||||
Single transfer (Batch) | L 50 × W 50 ~ L 750 × W 510 | ||||
Single transfer (2-positin) | L 50 × W 50 ~ L 350 × W 510 | ||||
Electric source | 3-phase AC 200, 220, 380, 400, 420, 480 V 2.0 kVA | ||||
Pneumatic source | 0.5 MPa, 200 L /min (A.N.R.) | ||||
Dimensions (mm) | W 1,280 × D 2,477 × H 1,444 | ||||
Mass | 2 390 kg (Only for main body:This differs depending on the option configuration.) | ||||
Placement head | Lightweight 16-nozzle head | 12-nozzle head | Lightweight 8-nozzle head | 3-nozzle head V2 | |
Max. speed | 38 500cph (0.094 s/ chip) | 32 250cph (0.112 s/chip) | 20 800cph (0.173 s/ chip) | 8 320cph (0.433 s/ chip) 6 500cph (0.554 s/ QFP) | |
Placement accuracy (Cpk≤1) | ±30 μm / chip (±25μm / chip*6) | ±30 μm / chip | ±30μm/chip ±30 μm/QFP 12mm to 32mm ± 50 μm/QFP 12mm Under | ± 30 μm/QFP | |
Component | 03015*7 *8/0402*7 chip ~ L 6 x W 6 x T 3 | 0402*7 chip ~ L 12 x W 12 x T 6.5 | 0402*7 chip ~ L 32 x W 32 x T 12 | 0603 chip to L 150 x W 25 (diagonal152) x T 30 | |
dimensions(mm) | |||||
Component supply | Taping | Tape : 4 / 8/ 12 / 16 / 24 / 32 / 44 / 56 mm | Tape : 4 to 56 mm | Tape : 4 to 56 / 72 / 88 / 104 mm | |
Max.120 (Tape: 4, 8 mm, Small real) | Front/rear feeder cart specifications : Max.120 ( Tape width and feeder are subject to the conditions on the left) Single tray specifications : Max.86 ( Tape width and feeder are subject to the conditions on the left) Twin tray specifications : Max.60 ( Tape width and feeder are subject to the conditions on the left) | ||||
Stick – | Front/rear feeder cart specifications : Max.15 (Single stick feeder) Single tray specifications : Max.15 (Single stick feeder) Twin tray specifications : Max.15 (Single stick feeder) | ||||
Tray – | Single tray specifications : Max.20 Twin tray specifications : Max.40 | ||||
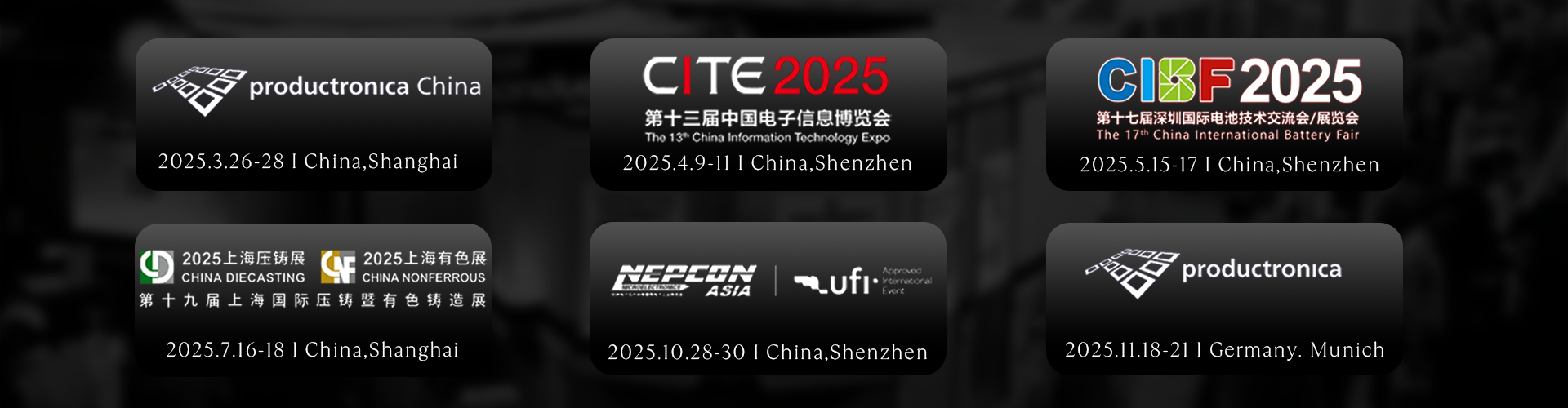