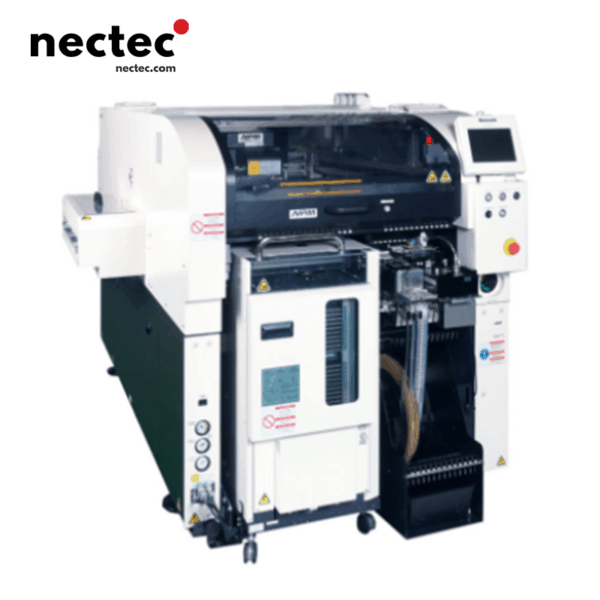
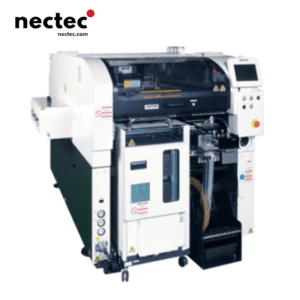
NPM-TT2 | High-Speed Odd-Form Components Placement Machine
The NPM-TT2 complements the NPM platform with frontand rear tray towers plus feeder slots for tape reels. ltstwin tray configuration enables independent mode. dual-lane production, Additionally, its dual-lane board handlingallows increased production of one or more productssimultaneously: yet,easily converts to single-lane modefor larger board sizes.
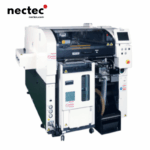
NPM-TT2 | High-Speed Odd-Form Components Placement Machine
- Description
Description
Placement Head System
8-Nozzle Multi-Function Head
- High-Versatility Placement Module: Optimized for high-volume standard component placement, achieving 18,000 CPH (0.20s/component) in PC format and 17,460 CPH (0.21s/component) in M format. Delivers ±40μm placement accuracy (Cpk≥1.0) for general-purpose components like 0603 chips.
3-Nozzle V2 Precision Head
- Odd-Form Component Specialist: Features 100N maximum placement force for complex geometries. Achieves ±30μm accuracy (Cpk≥1.0) for QFP packages, handling components from 0603 to 150×25×30mm (L×W×H, 152mm diagonal).
Vision Inspection System
Multi-Sensor 3D Metrology Module
- Integrated Z-Axis Imaging: Combines high-speed component alignment with vertical height measurement and coplanarity inspection. Enables stable recognition of micro-components (0201) and odd-form parts, ensuring sub-50μm placement precision and first-pass yield optimization.
Feeding System
Hybrid Component Supply Ecosystem
-
Multi-Modal Feeding Capability:
- Tape Feeding: Supports 4–104mm tape widths (4, 56, 72, 88, 104mm options).
- Tray Feeding: Front/rear units accommodate up to 40 trays (20 per side).
- Stick Feeding: Front/rear trays support 12 single sticks; feeder carts enable 28 stick feeders.
-
Modular Feeder Configuration: Quick reconfiguration via tray unit rearrangement or feeder cart exchange (e.g., “Batch Feeder Cart System”) reduces changeover time for high-mix production.
PCB Handling System
Dual-Lane/Single-Lane Flexibility
-
Single-Lane Mode:
- PC format: 50×50–510×590mm
- M format: 50×50–510×510mm
-
Dual-Lane Mode:
- PC format: 50×50–510×300mm
- M format: 50×50–510×260mm
-
Seamless Board Changeover:
- Dual-lane: Theoretically 0-second changeover (for cycle times ≤4.0s).
- Single-lane: 4.0-second changeover for single-sided PCBs.
Auxiliary Systems
Automated Production Continuity
-
Intelligent Material Logistics: Integration with automated storage systems (AS/RS) enables non-stop production via offline feeder setup and parallel changeover (e.g., monorail offline programming with trolley exchange).
-
Predictive Maintenance Suite (Optional):
- Auto-replaceable support pins reduce manual adjustment errors.
- Cloud-connected diagnostics identify worn feeders/nozzles, sending maintenance recommendation lists via IoT.
specification
Model | Panasonic NPM-TT2 | ||
PCB dimensions | PC size | Single-lane mode | L50mmxW50mm-L510mmxW590mm |
Dual-lane mode | L50mmxW50mm-L510mmxW300mm | ||
M sizze | Single-lane mode | L50mmxW50mm-L510mmxW510mm | |
Dual-lane mode | L50mmxW50mm-L510mmxW260mm | ||
PCB exchange time | Single-lane mode | 4.0s(With no component mounted on the reverse side of PCB) | |
Dual-lane mode | 0S*”No Os when cycle time is 4.0 s or less | ||
Electric source | 3-phase AC 200,220,380.400.420.480 V 2.5 KVA | ||
Pneumatic source | Min.0.5 MPa、200 L/min (A.N.R.) | ||
Dimensions | W1300mm xD2798mm xH1444mm | ||
Mass | 2 690 kg(Only for main body:This differs depending on the option configuration.) | ||
Placement head | Lightweight 8-nozzle head(Per head) | 3-nozzie head v2*6(Per head) | |
Pacement | PC size | 18 000 cph (0.20 s/chip) | 7 200 cph(0.50 s/chip) |
Speed | 5 900 cph(0.61 s/QFP) | ||
Pacement | M sizze | 17 460 cph (0.21s/chip) | 6 984 cph(0.52 s/chip) |
Speed | 5 723 cph(0.63 s/QFP) | ||
Placament accuracy (Cpk≥1) | ±40um/chip | ±40um/chip | |
±30μm/QFP □12mm ~□32mm | ±30μm/QFP | ||
±50μm/QFP □12mmUnder | |||
Component dimensions (mm) | 0402chip*6 to L32 xW32 xT12 | 0603chip-L150xW25(diagonal152)xT30 | |
Compcnent supply | Taping | Tape:4 to 56/72mm | Tape:4 to 56/72/88/104mm |
Specifications for front/rear tray feeders :Max.52 | |||
Specifications for front/rear feeder carts :Max.120(Tape:4、8 mm) | |||
Stick | Specifications for front/rear tray feeders:Max.12 (Single stick feeder) | ||
Specifications for front/rear feeder carts:Max.28 (Single stick feeder) | |||
Tray | Max.40 (Front supply unit : Max. 20 + Rear supply unit : Max. 20) |
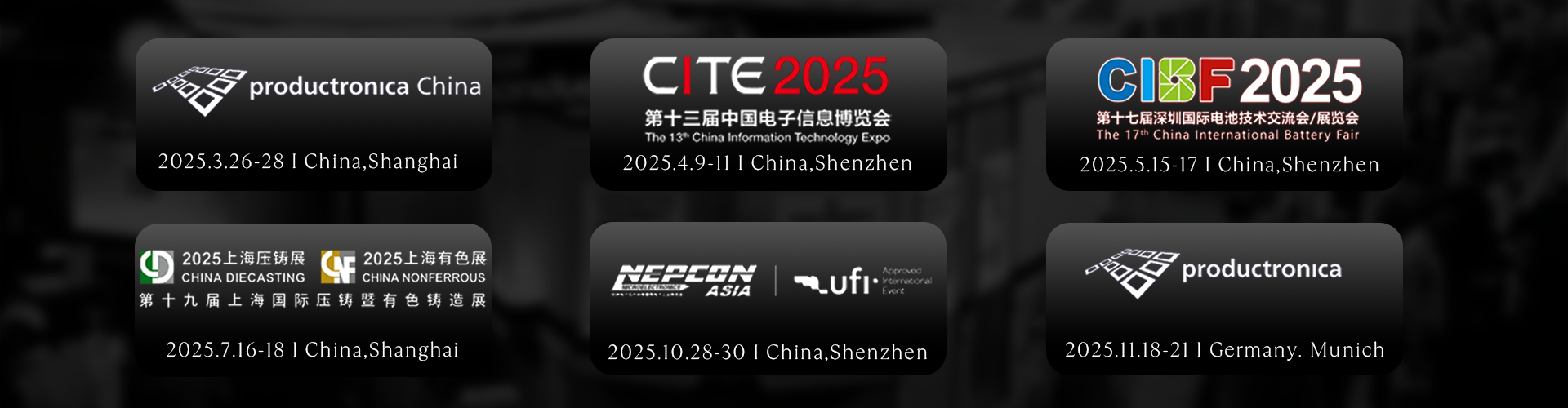