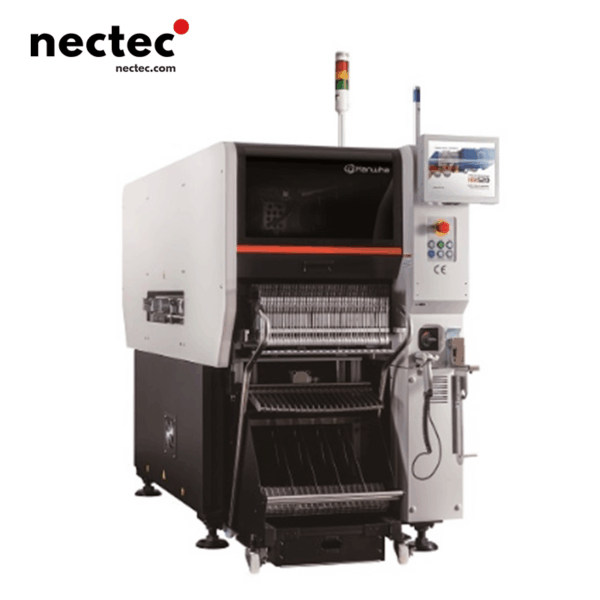
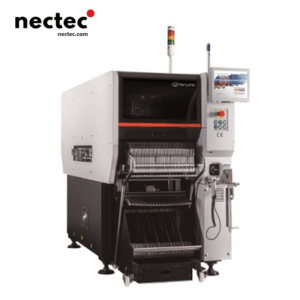
HM520 | Cutting-edge Modular Mounter
Introducing the HM520, Hanwha’s Cutting-edge Modular Mounter.It have 2 Gantries and 20 Spindles to achieve speed of 80000 CPH.The accuracy of the machine is about ±25 μm [Cpk ≥ 1.0 (Chip)].And its dimension is 890* 2,370*1,930(L*D*H,Unit: mm).
Category: Hanwha
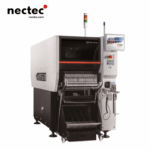
HM520 | Cutting-edge Modular Mounter
In stock
- Description
Description
Placement Performance
- Throughput Capability:
- Maximum placement speed: 80,000 CPH (ideal conditions), achieved via dual gantry architecture with 20 independent spindles in synchronized operation.
- Positional Accuracy:
- Standard components (e.g., 0201): ±25μm (Cpk≥1.0)
- IC components (e.g., QFP/BGA): ±30μm (Cpk≥1.0)
- Component Handling Range:
- Supports 0201 metric (0.25×0.125mm) to 55×55mm components (max height 15mm), including microchips, LEDs, and fine-pitch packages (QFP/BGA).
Vision System
- In-Flight Vision Technology:
- Real-time component recognition during head transit reduces idle time and enhances throughput efficiency.
- High-Resolution Imaging Module:
- 5MP camera enables precise alignment of micro-components (e.g., 0402, 0603).
- Side View Inspection System:
- Monitors nozzle condition and component orientation in real-time to prevent misplacement or omissions.
- Optional 3D Laser Profiling: Detects component height and coplanarity to mitigate cold solder and tombstoning defects.
Feeder System
- Powered Feeder Platform:
- Supports 8–56mm tape feeders, tube/tray components, with 120-station capacity (8mm tape equivalent).
- Intelligent Feeding Technology:
- Automatic tape splicing and real-time material shortage alerts minimize manual intervention for uninterrupted production.
Motion Control System
- Dual Gantry Linear Motor Drives:
- Micron-level X/Y axis resolution with vibration dampening algorithms ensures high-speed placement stability.
- Adaptive Force Modulation:
- Dynamic pressure adjustment by component type prevents damage to sensitive devices (e.g., fine-pitch ICs).
Software & Intelligent Functions
- Dynamic Trajectory Optimization:
- Auto-allocates component placement sequences to reduce gantry idle travel and enhance efficiency.
- Family-Based Changeover:
- Shared feeder/nozzle libraries across similar machines reduce changeover time by 40% for 同族 products.
- Defect Mark Sharing:
- Cross-equipment Badmark data sharing shortens overall production cycle by preemptively addressing recurring issues.
specification
[wptb id="8559" not found ]
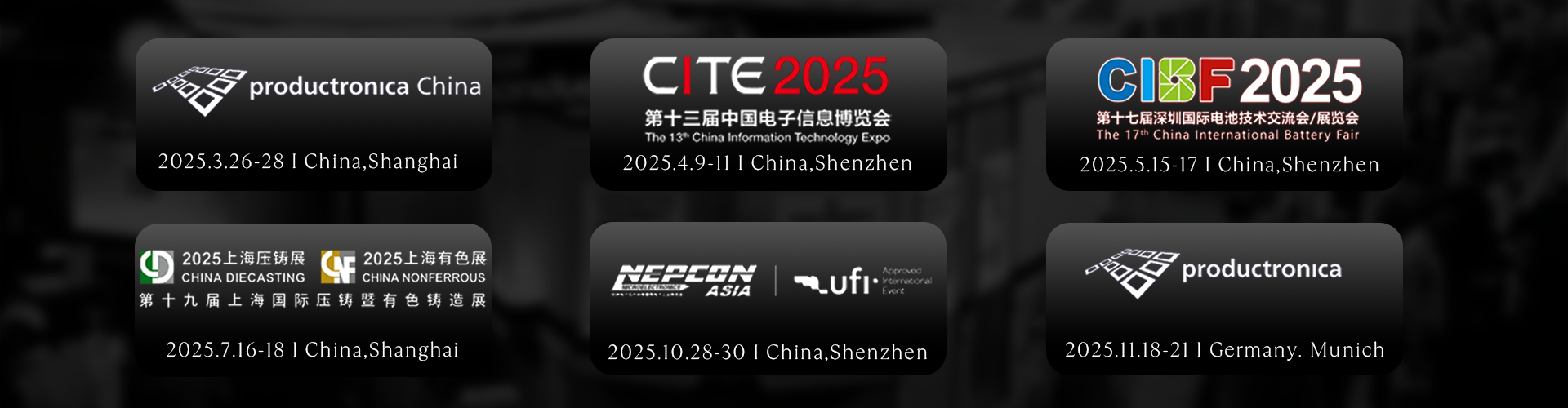