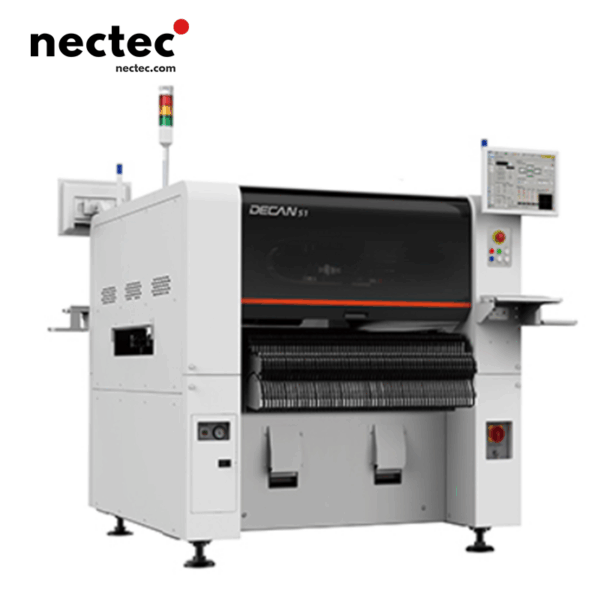
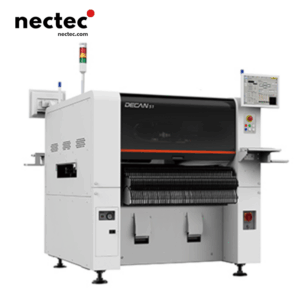
DECAN-S1 | Fast & Flexible Mounter
Introducing the DECAN-S1, Hanwha’s Fast & Flexible Mounter.It have 1 Gantry and 10 Spindles to achieve speed of 47000 CPH.The accuracy of the machine is about ±28 μm [Cpk≥ 1.0 (Chip)] or ±30 μm [ Cpk≥ 1.0 (IC)].And its dimension is 1,430*1,740*1,485(L*D*H,unit:mm).
Category: Hanwha
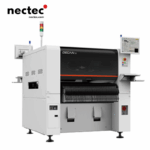
DECAN-S1 | Fast & Flexible Mounter
In stock
- Description
Description
Conveyor System
- Substrate Handling Capability:
- Supports standard PCB sizes from 50×50mm to 510×460mm, compatible with flexible and rigid board transport.
- Base dual-track design with servo-motor-driven conveyance ensures stability, featuring the cost-optimized omission of advanced magnetic levitation technology.
Vision System
- Fiducial Alignment Module:
- Basic PCB positioning via 2D camera with fiducial mark recognition, achieving ±28μm positional accuracy (in contrast to DECAN S2’s ±25μm).
- Component Centering Vision:
- Supports 0402 metric (0.4×0.2mm) and larger components; 3D laser inspection module available as optional upgrade (not standard).
Placement Head
- Single Cantilever Architecture:
- 6 independent spindles deliver a theoretical throughput of 47,000 CPH (vs. S2’s 92,000 CPH), suited for medium-throughput production.
- Adaptive Force Control:
- Programmable placement pressure adjustment for conventional components (e.g., resistors, capacitors) and small ICs (e.g., QFP packages).
Feeder System
- Powered Feeder Platform (eFeeder):
- Supports 8–44mm tape feeders and tube components with 80-station capacity (vs. S2’s 120 stations).
- Basic Material Management:
- LED-based tape residue alerts; lacks integrated automatic material splicing functionality.
Motion Control System
- Servo-Driven Mechanics:
- X/Y axes utilize traditional lead screw drives with ±30μm positioning accuracy (vs. linear motor’s ±25μm).
- Software-Based Vibration Mitigation:
- Acceleration profile optimization maintains stability, though high-speed operation may require throughput reduction for consistency.
Software & Operational Interface
- Manual Path Optimization:
- Supports manual component grouping and placement sequence adjustment; lacks real-time dynamic optimization algorithms.
- Basic Fault Diagnostics:
- Predefined error code library (e.g., nozzle clogging, feeder jams) without integrated remote monitoring capabilities.
specification
CPH (Optimal) | 47’000 |
Smallest Component (Metric) | 0.3mm x 0.15mm |
Largest Component Handling | 55mm square, 75mm long connector |
Component Height Maximum | 15mm |
Placement Accuracy | ±28um |
PCB Size (Maximum) | 510mm x 510mm |
PCB Size (Minimum) | 50mm x 50mm |
PCB Size (Optional) | 1500mm x 510mm |
Feeder Capacity (8mm) | 120 |
Gantry Type | Single (10 Spindles) |
Conveyor Type (Standard) | 3 Stage (Single) |
Conveyor Type (Optional) | N/A |
Alignment Type | Flying Vision + Stage Vision |
Feeder Type | Pneumatic + Electric |
Gripper Use | N/A |
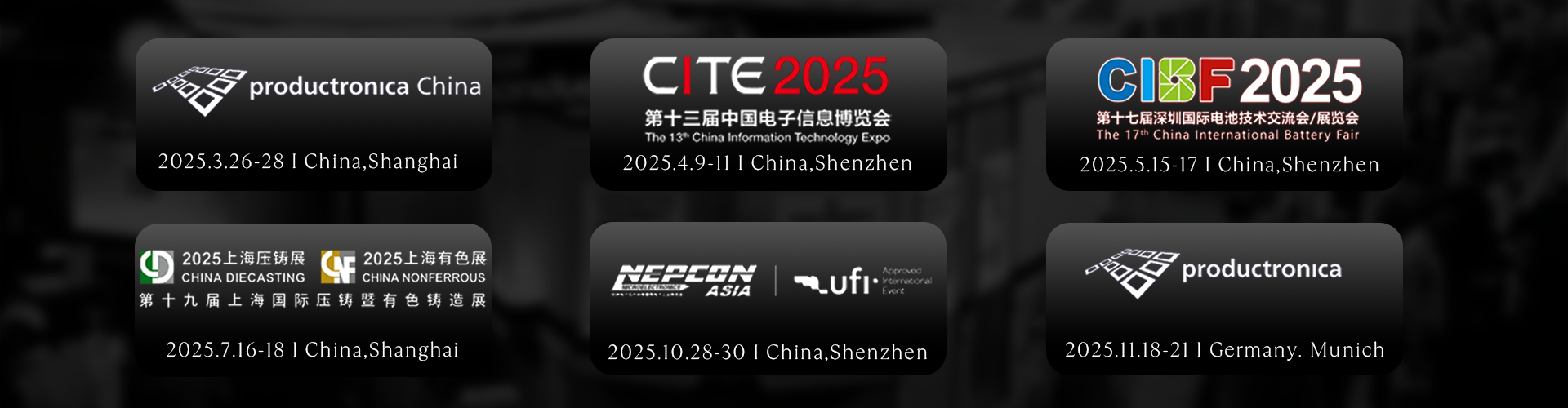